PurGo Transforms Waste Glass Recycling Business Through Improved Business Insight
Founded in 1922 Berryman now URM (UK Ltd) is the UK’s largest purchaser and recycler of waste glass, with an extensive network of bottle banks and collection depots throughout UK. The company brings in kerbside and trade glass, along with glass output from MRF’s and operates world-class waste glass treatment plants.
In 2016 URM decided to implement an Enterprise Resource Planning (ERP) system into its business with the aim of standardising and streamlining all processes and creating transparency across every area of the business.
A Seamless ERP System
Steve Dixon, Project and Systems Manager, URM (UK) Ltd said: “We went through a tender process and invited shortlisted companies, including VWS Software Solutions, to come back and present their system. We scored each offering and PurGo from VWS scored higher than the rest.”
“Two things stood out with PurGo and VWS. Firstly flexibility, VWS was happy to develop the system with us and for us, to meet our exact business needs. We were looking for a partner and that’s exactly what they offered. Secondly the reporting structure is great. There are over 40 reporting structures, which enables us to have complete transparency across the business.”
PurGo is an ERP (Enterprise Resource Planning) software system designed for waste management & recycling operators and materials processing facilities that integrates seamlessly with other business systems and software packages.
The software and interface are highly automated, exception driven and most importantly intuitive and user friendly.
Phased Integration
URM has introduced PurGo into the business in stages, department by department, starting with Transport & Logistics.
Drivers now use PurGo PDA’s to log on, do vehicle checks, send data back from weigh bridges, and record weight and location data from collections. The system also allows details about collections to be sent directly to third party hauliers.
The URM Workshop now uses PurGo software to facilitate the management of vehicles, repairs, servicing and inspection schedules; and Purgo integrates with the finance department’s existing accounts packages to produce accurate invoicing and financial reporting.
The system is currently being phased into the Production area of the business, involving the complex integration of 4 glass processing sites, two of which have already been completed.
PurGo’s production module caters for the management of processing plants such as Materials Recycling Facilities (MRF) and Mechanical Biological Treatment (MBT) plants. PurGo allows for the control and monitoring of material flow from feedstock through sorting equipment to end-products and waste. The system monitors the speed, efficiency, profitability and performance of processing (down to shift and operator level) enabling the proper planning of shifts and staffing, as well as monitoring the performance of one shift against another. It also measures the quality of the product and monitors the performance of the equipment including downtime and any service scheduling. There are over 40 different reports available for this module alone.
Andy Mirecki, VWS Software Solutions Ltd: “URM’s processing plants are state of the art facilities, the best in the world really. It is really great to be able to work with them on such high-tech equipment.”
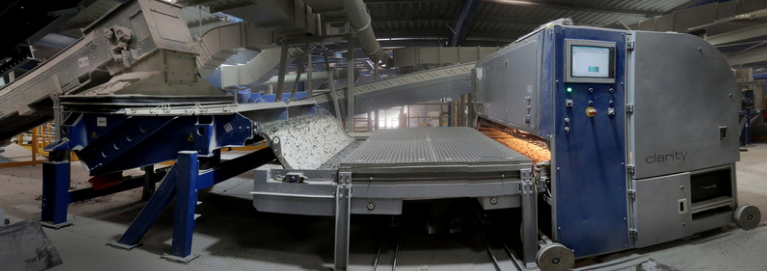
Removing The Single Points of Failure
Continued Steve: “Not only does PurGo standardise processes and procedures; it also defines roles and responsibilities. A certain number of inputs are required at each stage of the process and only once they are carried out is the task deemed complete. There are no grey areas.”
Additional benefits of PurGo include the ability to remove the ‘Single Point Of Failure’ situation. By using the same processes across every area of the business staff can move more easily from one department to another, or from one job to another.
Continuous Development
PurGo now also includes a browser-driven Sales CRM module that can be accessed using any device. URM Account Managers situated around the UK are able to input and access customer information, record all activity and contract details.
In addition, the PurGo team are working on a number of further developments and additional services specifically for URM. For example a Quality module will tie in with production to test and measure materials coming in, and products going out, against benchmark quality levels. A live Materials Management component involving the incorporation of weighing technology into large shovels will provide a live record of the movement of stock from different bays to hoppers.
Further possible areas for future development include Human Resources, Safety and Engineering.
Feeling The Benefits
Steve Dixon: “In a matter of weeks we noticed the benefits. PurGo has given us a far more detailed understanding of what drives our business performance. Everything we do is now linked and transparent. We have become an almost entirely paperless operation, so the margin for error is much smaller.”
“PurGo is great for exception reporting. If one of our drivers turns up to collect a bin or change a skip and they can’t gain access they take a picture of the site with locked gates using the PurGo PDA’s, and we can charge for the visit.”
Steve continued: “Our customer service has improved drastically even the way we answer the phone. PurGo requires everyone to be accountable, every call to be logged, and deadlines to be made and achieved.”
“PurGo has transformed our business by creating transparency across all departments. All the reporting is now standardised via PurGo and there is only one ‘truth’ not 5 or 6 different versions of it.”